What is Safety Testing?
Safety testing is a method of testing electrical and electronic products to ensure that they comply with relevant safety standards and legal requirements. Conducting safety testing during product design and manufacturing can reduce potential safety risks, thereby ensuring personal and property safety.
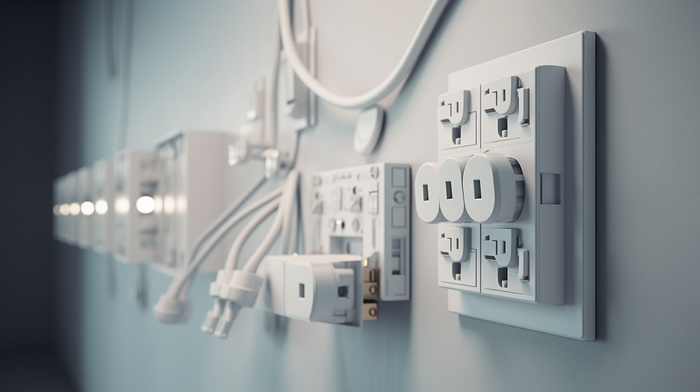
Safety testing includes various tests, mainly including the following:
1. Electrical safety testing:
Electrical safety testing is a test of electrical products aimed at ensuring that the insulation and grounding of the product meet relevant safety standards and legal requirements. Electrical products usually involve material properties such as voltage and current. If these properties do not meet standards, they can pose a safety hazard to personnel and property. Therefore, conducting electrical safety testing of electrical products is very important.
Electrical safety testing usually includes the following test items:
a). Insulation testing: Insulation testing mainly checks the insulation performance of electrical products to ensure that the insulation resistance between potential is higher than the relevant standard requirement under normal working conditions, to prevent electrical leakage.
b). Grounding test: The grounding test requires that certain metal components of the internal or external of the electrical product must be connected to the grounding system, so that when a fault occurs, the contact voltage of the person meets the standard range, avoiding accidents such as electric shock.
c). Leakage current test: The leakage current test mainly detects whether the system has leakage under normal working conditions of electrical products, and its magnitude, to avoid accidents such as electric shock.
d). Withstand voltage test: The withstand voltage test is a test of equipment, products, parts and other components that resist high voltage electrical equipment to test whether it is safe. Depending on the different certification schemes, the objects of testing can be all circuits, capacitors, insulation materials, transformers, equipment, low-voltage switch breakers, etc.
The above testing items can ensure the safety of electrical products, provide consumers with more reliable and safe electrical products, and also help to eliminate substandard goods and counterfeit and shoddy products, and improve market supervision.
2. Mechanical safety testing:
Mechanical safety testing refers to a series of tests on mechanical products aimed at ensuring that product structure, casing, interface, etc. comply with relevant safety standards and legal requirements, to ensure personal and property safety. Mechanical safety testing can ensure product quality and safety, and avoid unnecessary losses and injuries.
Mechanical safety testing usually includes the following test contents:
a). Casing protection level test: Test whether the product case can effectively protect the internal components and users, avoiding external object or personal injury.
b). Operating noise test: Test whether the noise emitted by the mechanical product during normal operation exceeds the specified standard limit value, avoiding negative impacts on personnel and environment.
c). Mechanical shock test: Test whether the product possesses sufficient shock resistance, can withstand the designed range of shock loads.
d). Mechanical strength test: Test whether the mechanical strength of the product complies with the standard, whether it can maintain product stability and durability for a long time under normal working load.
e). Gravity test: Test whether the product can work properly within the specified angle range, avoiding overturning, tilting and other situations due to operating errors.
Mechanical safety testing can help manufacturers improve product quality and safety, avoid injuries or losses caused by defects in mechanical design and processes, and has a significant role in market supervision to curb the circulation of counterfeit and substandard products.
3. EMC testing:
EMC testing is a method of testing electrical and electronic products to ensure that the product does not produce electromagnetic interference during operation, and can also resist external electromagnetic radiation and interference to ensure product stability and reliability. EMC testing is part of electrical safety testing and an important guarantee for electronic products to comply with relevant safety standards.
EMC testing generally includes the following aspects:
a). Electromagnetic compatibility testing: Test whether electronic products have mutual interference with their surrounding electromagnetic environment and whether they can work normally under this environment.
b). Radiation interference testing: Test whether the product emits electromagnetic waves to the surrounding area, causing interference and impact on other equipment and systems.
c). Anti-interference testing: Test whether electronic products can resist the impact of external electromagnetic interference, and whether they have corresponding capabilities and stability.
d). Conducted interference testing: Test whether there is a conductive path of electromagnetic interference inside the product, and whether performance is affected.
The purpose of EMC testing is to ensure that electronic products can always maintain a stable working state in various application scenarios, without causing interference and impact on other electronic equipment and systems, and also to make products have the ability and stability to resist external electromagnetic interference, ensuring that their performance and quality comply with relevant safety standards and legal requirements.
4. Chemical substance testing:
Chemical substance testing is a test of the materials used in electrical and electronic products. The test aims to ensure that all materials used in the product do not contain harmful chemical substances for human beings and the environment. Common materials used in electrical and electronic products include plastics, metals, rubber, etc. During product production, these materials may be polluted or contaminated by other harmful substances. Therefore, chemical substance testing has become an important link to ensure product quality and safety.
In fact, the key to chemical substance testing mainly lies in the following aspects:
a). Heavy metal content testing: Testing whether harmful heavy metals such as lead, cadmium, and mercury are contained in electrical and electronic products. These harmful substances can cause great harm to human health.
b). Halogen content testing: Halogen compounds cannot be treated by ordinary garbage disposal methods and pose a threat to environmental philosophy. They are mainly dealt with through emissions and landfill.
c). Flame retardancy test: Test whether the material has flame retardancy, and whether it can prevent fires in potential use environments, ensuring personal and material safety.
d). Other content testing: Test the content of harmful substances such as formaldehyde, benzene, plasticizers, and whether they can meet relevant standards and production requirements.
In addition to the above testing items, attention should also be paid to the environmental and sustainability of chemical substances to ensure that product materials come from environmentally friendly and sustainable development materials. Chemical substance testing can ensure product quality and safety, prevent the use of harmful substances, protect the environment, strengthen market supervision, and is also one of the responsible behaviors towards consumers.
These tests have a wide range of applications. For example, in the fields of home appliances, automotive electronics, medical equipment, aerospace, etc., safety testing is required to ensure product quality and safety. At the same time, safety testing can also serve as a means of supervising quality during the product engineering research and development and manufacturing process, improving production efficiency and product quality.
In addition, for electrical and electronic products that need to be imported for sales abroad, they often need to comply with local safety standards and legal requirements. Conducting safety testing can ensure that the products comply with local regulations, to avoid market loss and legal risks due to failure to pass the test.
In today's fiercely competitive market, consumers are paying more and more attention to the safety and quality of products. Products that have undergone safety testing have higher reliability and credibility, and can obtain better market feedback and user reputation. Therefore, safety testing has become an essential part of modern product design and manufacturing.